Leistungsstarke digitale Tools, für Code-Profis und Einsteiger
Vernetzen Sie Abteilungen und Softwarelösungen miteinander
Verabschieden Sie sich von Datensilos und Softwarelösungen, die nicht miteinander kommunizieren können. Mit Intrexx leiten Sie Datenströme exakt dahin, wo sie gebraucht werden.
Entwickeln Sie eigene Anwendungen in Rekordzeit
Maßgeschneiderte Applikationen für Ihr Unternehmen entwickeln Sie einfach selbst – mit wenigen Klicks und abgestimmt auf Ihre Bedürfnisse.
Intrexx erleben
Intrexx wurde von Menschen für Menschen entwickelt. Mit unserer benutzerfreundlichen Low-Code-Plattform entwickeln Sie Applikationen für Ihr Unternehmen in kürzester Zeit.
Sie brauchen Starthilfe in Sachen Digitalisierung? Setzen Sie auf unsere Experten!
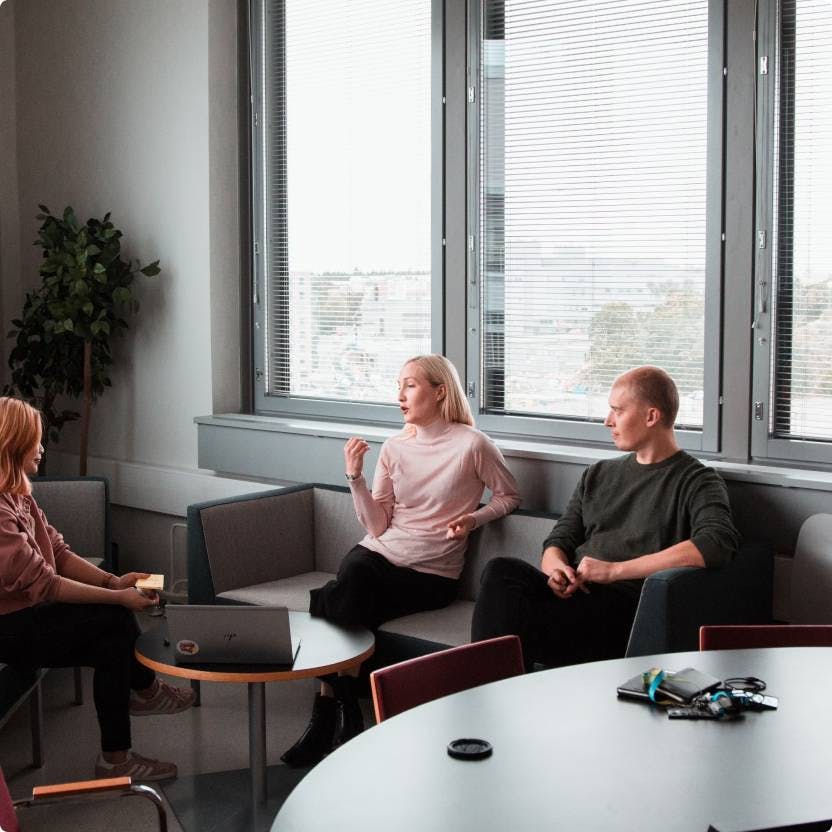
1,2+ Mio.
Zufriedene Nutzer
70.000+
Entwickelte Anwendungen
25+
Jahre am Markt
Gestalten Sie die Digitalisierung in Ihrem Unternehmen. Mit den Tools von Intrexx.
Mit Intrexx kanalisieren Sie Datenströme, automatisieren Prozesse und führen beides in maßgeschneiderten Applikationen zusammen – mit minimalem Programmieraufwand.
Übernehmen Sie die Kontrolle über Ihre Prozesse.
Digitalisieren, optimieren und vereinfachen Sie Abläufe in Ihrem Unternehmen.
Prozess-BuilderFühren Sie alle Ihre Daten auf einer Plattform zusammen.
Vernetzen Sie Daten aus Softwarelösungen, Datenbanken und aus jeglichen Schnittstellen miteinander.
Daten-BuilderRealisieren Sie individuelle Anwendungen für Ihr Business.
Von einfachen Apps zur Erfassung von Umfragen bis hin zu komplexen Dashboards, die Ihre Geschäftsprozesse visualisieren.
Applikations-BuilderIn Intrexx steckt alles, was Sie für die digitale Transformation benötigen.
Beschleunigen Sie Ihre digitale Transformation mit der Low-Code-Plattform Intrexx. Das Entwickeln von individuellen Unternehmensapplikationen erfolgt in kürzester Zeit.
Mehr erfahrenDurch Low-Code entstehen professionelle Apps mit minimaler Programmierung.
Unsere deutsche Cloud ist ISO 27001 zertifiziert und DSGVO-konform. Ein feinteiliges Rechtesystem stellt sicher, dass Mitarbeiter nur Inhalte einsehen können, die für sie bestimmt sind.
Mehr erfahrenBleiben Sie auf der sicheren Seite und behalten Sie den Überblick über Nutzer.
Stellen Sie sicher, dass alle Abteilungen stets auf die aktuellsten Daten Zugriff haben. Dabei können Sie problemlos an bestehende Datenknoten anknüpfen.
Mehr erfahrenIntegrieren Sie Daten aus bestehenden Kernsystemen, Datenbanken und noch mehr.
Übernehmen Sie die Kontrolle Ihrer Daten. Intrexx können Sie sowohl auf Ihrer eigenen Infrastruktur hosten, als auch auf unserer leistungsstarken Cloud.
Mehr erfahrenSie entscheiden, wo Ihre Daten liegen. Ob bei Ihnen oder in der Intrexx Cloud.
Intrexx ermöglicht die Entwicklung digitaler Arbeitsabläufe. Automatisieren Sie individuell angepasste Prozesse und sparen Sie wertvolle Zeit.
Mehr erfahrenAutomatisieren Sie redundante und kritische Prozesse im Handumdrehen.
Stellen Sie Ihre Unternehmensdaten auf übersichtlichen Dashboards dar und optimieren Sie Entscheidungsprozesse durch automatisierte Analysen.
Mehr erfahrenGestalten Sie visuelle Dashboards und werten Sie Daten in Windeseile aus.
Durch Low-Code entstehen professionelle Apps mit minimaler Programmierung.
Bleiben Sie auf der sicheren Seite und behalten Sie den Überblick über Nutzer.
Integrieren Sie Daten aus bestehenden Kernsystemen, Datenbanken und noch mehr.
Sie entscheiden, wo Ihre Daten liegen. Ob bei Ihnen oder in der Intrexx Cloud.
Automatisieren Sie redundante und kritische Prozesse im Handumdrehen.
Gestalten Sie visuelle Dashboards und werten Sie Daten in Windeseile aus.
Beschleunigen Sie Ihre digitale Transformation mit der Low-Code-Plattform Intrexx. Das Entwickeln von individuellen Unternehmensapplikationen erfolgt in kürzester Zeit.
Mehr erfahrenDurch Low-Code entstehen professionelle Apps mit minimaler Programmierung.
Unsere deutsche Cloud ist ISO 27001 zertifiziert und DSGVO-konform. Ein feinteiliges Rechtesystem stellt sicher, dass Mitarbeiter nur Inhalte einsehen können, die für sie bestimmt sind.
Mehr erfahrenBleiben Sie auf der sicheren Seite und behalten Sie den Überblick über Nutzer.
Stellen Sie sicher, dass alle Abteilungen stets auf die aktuellsten Daten Zugriff haben. Dabei können Sie problemlos an bestehende Datenknoten anknüpfen.
Mehr erfahrenIntegrieren Sie Daten aus bestehenden Kernsystemen, Datenbanken und noch mehr.
Übernehmen Sie die Kontrolle Ihrer Daten. Intrexx können Sie sowohl auf Ihrer eigenen Infrastruktur hosten, als auch auf unserer leistungsstarken Cloud.
Mehr erfahrenSie entscheiden, wo Ihre Daten liegen. Ob bei Ihnen oder in der Intrexx Cloud.
Intrexx ermöglicht die Entwicklung digitaler Arbeitsabläufe. Automatisieren Sie individuell angepasste Prozesse und sparen Sie wertvolle Zeit.
Mehr erfahrenAutomatisieren Sie redundante und kritische Prozesse im Handumdrehen.
Stellen Sie Ihre Unternehmensdaten auf übersichtlichen Dashboards dar und optimieren Sie Entscheidungsprozesse durch automatisierte Analysen.
Mehr erfahrenGestalten Sie visuelle Dashboards und werten Sie Daten in Windeseile aus.
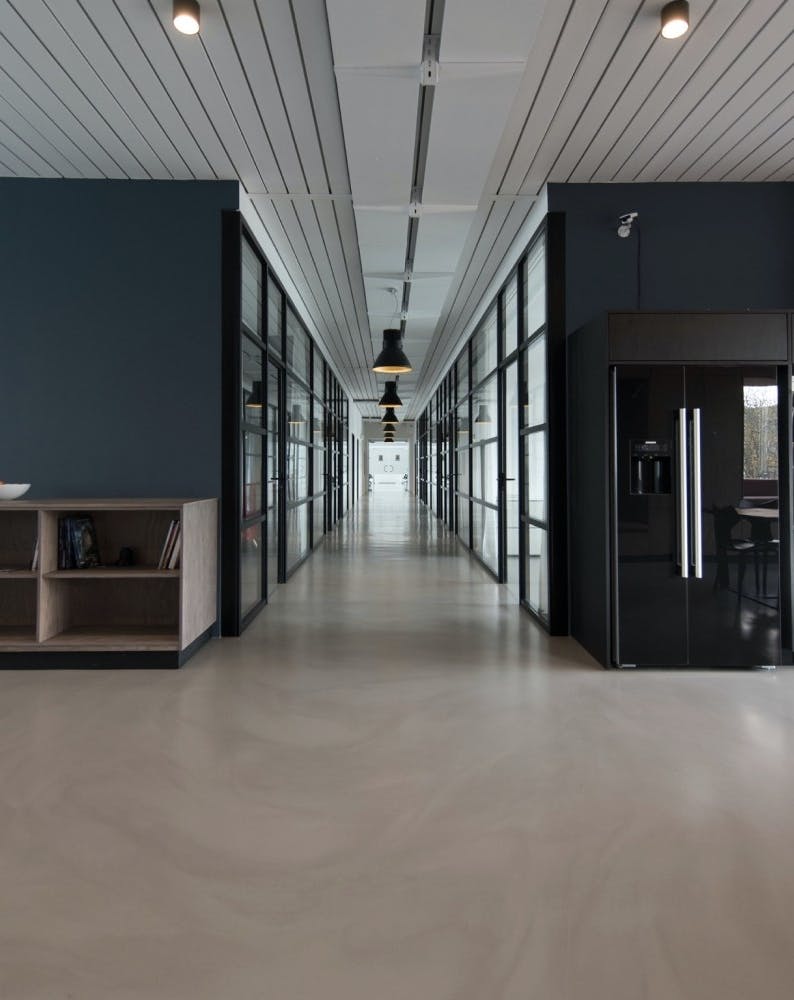
Pohl-Boskamp
Wir haben ein flexibles Intranetportal gesucht, mit dem wir Workflows digital abbilden und unsere bestehenden Systeme unkompliziert anbinden können. Hier gibt es meiner Meinung nach keine ernsthafte Alternative zu Intrexx.
Noch mehr Unternehmen, die mit Intrexx erfolgreich digitalisiert haben.
SPIE
Zentrales Kundenmanagement für mehr als 100 Standorte
Mit Intrexx wurde ein individuelles CRM-System etabliert, das den gesamten Angebotsprozess automatisiert.
Euregio-Klinik
Effizientes Dokumentenmanagement für den Klinikalltag
Die Euregio-Klinik spart mit Ihrem neuen Klinikportal Zeit und Geld – durch eine optimierte Verwaltung von Dokumenten.
BETTENRID GmbH
Digitales Reklamationsmanagement senkt Bearbeitungszeit um 30%
Bettenrid setzt der Zettelwirtschaft ein Ende. Mit Intrexx entstand ein abteilungsübergreifendes Portal, das die gesamte Prozesskette abbildet.
Seit über 25 Jahren helfen wir der Digitalisierung auf die Sprünge. In sämtlichen Industrien.
Seit über 25 Jahren helfen wir der Digitalisierung auf die Sprünge. In sämtlichen Industrien.
Dirigieren Sie Ihre Digitalisierung
Potenzielle Bereiche für eine effiziente Digitalisierung im Unternehmen zu finden, kann eine echte Herausforderung sein. Vereinbaren Sie jetzt einen Termin mit unseren Experten und lassen Sie sich beraten, wie eine Lösung für Ihre Anforderungen aussehen kann.
Mit Intrexx können Sie bequem loslegen. Auch ohne eigene IT-Abteilung.
Sie entscheiden, ob Sie selbst entwickeln wollen oder die Aufgabe in unsere Hände legen. In jedem Fall steht Ihnen die Low-Code-Plattform von Intrexx immer zur Verfügung.
Lehnen Sie sich zurück – Wir entwickeln für Sie.
Gemeinsam identifizieren wir die zu digitalisierenden Prozesse in Ihrem Unternehmen und entwickeln passgenaue Lösungen.
- Teams ohne interne IT-Ressourcen
- Zeitsparende Entwicklung
- Testen von Digitalisierungsmöglichkeiten
Übernehmen Sie das Ruder und entwickeln Sie selbst.
Hat Ihre Organisation einen IT-Hintergrund und ein gutes Verständnis für die internen Prozesse? Entwickeln Sie selbstständig Low-Code Lösungen mit Intrexx!
- IT-Abteilungen
- Organisationen mit striktem Digitalisierungsplan
- Sehr individuelle Prozesse
Ob wir entwickeln oder Sie selbst– von der Intrexx Plattform profitieren Sie immer.
Bringen Sie Daten zusammen, digitalisieren Sie Prozesse und entwickeln Sie individuelle Anwendungen.
Intrexx Plattform entdecken